CNC machining is like a super-skilled craftsman, effortlessly tackling tough tasks. Combining CNC with PC boards is like pairing a master swordsman with a legendary blade—unstoppable!
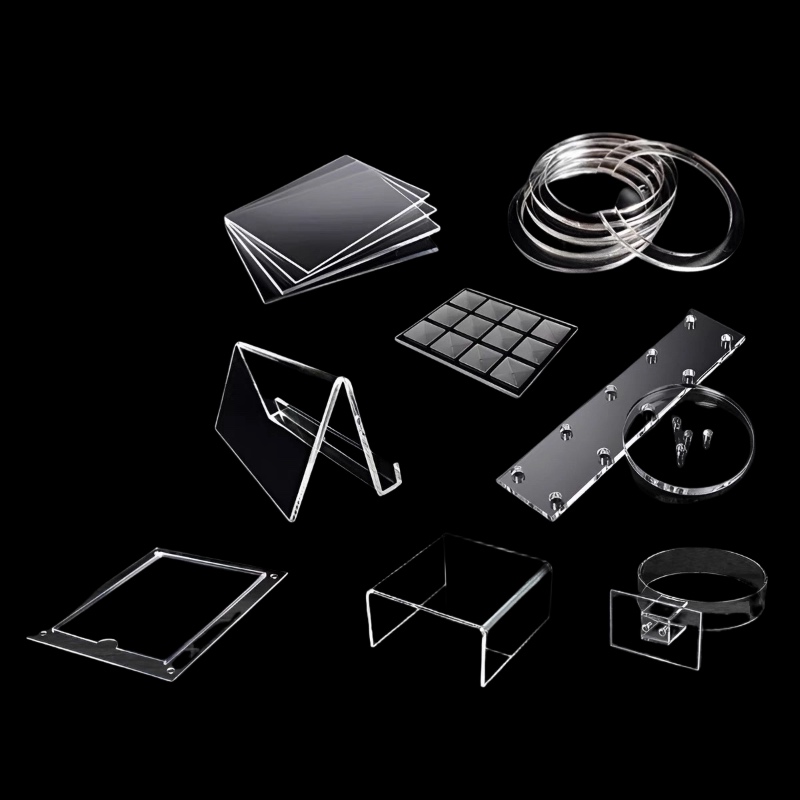
When machining PC insulating boards with CNC, there are several key points to keep in mind.
First, tool selection is critical. PC boards are relatively soft, so sharp, high-quality cutting tools are essential to avoid burrs and ensure a smooth surface. High-speed steel or carbide tools work well. Spindle speed also matters: too fast, and the board may overheat and warp; too slow, and efficiency drops while repeated friction risks damaging the board.
Next, machining parameters need fine-tuning. Feed rate must be balanced—too high, and the tool may break or crack the PC board; too low wastes time. Cutting depth is equally important: excessive depth risks piercing or ruining the board, while insufficient depth fails to meet requirements.
The workshop environment also plays a role. PC boards are sensitive to static electricity, so maintaining moderate humidity is crucial. A dry environment can attract dust via static, harming precision, or even cause electrostatic discharge (ESD) damage. Temperature control is vital too—excessive heat softens and warps PC boards.
Lastly, securing the board requires even clamping force. Over-tightening distorts the board, while loose fixation leads to shifts during machining, compromising dimensional accuracy.
In short, every step demands attention to produce high-quality PC boards.